With HP Backup & Recovery Manager, you can quickly recover and get back to work when information is accidentally deleted or your operating system is corrupted. The fbw file contain split backup. This fbw file type entry was marked as obsolete and no longer supported file format. This type of file is no longer actively used and is most likely. Description: FBW file is a HP Backup Segment. HP provides free data and system file protection for its business desktops, notebooks, and workstations (HP Backup and Recovery Manager). The.FBW file format is used by the HP system recovery backup utility to create backups of user data. Once the backup is complete, your selected data is stored within the.FBW files and should now be.
- Now, my minwinpc files did not have any 0's in them, only Backup.1 and Backup.2.fbw. I was able to extract to C drive HOWEVER, it's all blank. The folders are there but when I open them they are.
- FBW format was developed for Windows Server 2003 and 2008 systems as a part of business-oriented data backup solution. FBW is an archive file that stores data in compressed form. FBW files were typically used as security backup copies and stored on external storage devices (CDs, USB drives, external HDD drives, etc.).
Fly-By-Wire
From SKYbrary Wiki
Article Information | ||
---|---|---|
Category: | Flight Technical | |
Content source: | SKYbrary | |
Content control: | SKYbrary |
Description
Fly-by-Wire (FBW) is the generally accepted term for those flight control systems which use computers to process the flight control inputs made by the pilot or autopilot, and send corresponding electrical signals to the flight control surface actuators. This arrangement replaces mechanical linkage and means that the pilot inputs do not directly move the control surfaces. Instead, inputs are read by a computer that in turn determines how to move the control surfaces to best achieve what the pilot wants in accordance with which of the available Flight Control Laws is active.
Why it is useful
The advantages of reduced weight, improved reliability, damage tolerance, and more effective control of a necessarily highly manoeuverable aircraft, were first recognised in military aircraft design. The first aircraft to have FBW for all its flight controls in place of direct mechanical or hydraulically-assisted operation, was the F-16 in 1973. In the context of military fast jet need for agility, and therefore relatively more unstable aircraft, FBW provides the ability to ensure that unintended increases in angle of attack or sideslip are detected and rapidly, and automatically, resolved by marginally deflecting the control surfaces in the opposite way while the problem is still small. FBW also enables highly reliable flight envelope protection systems which, provided the FBW system functions at its normal level, significantly enhances safety.
How it Works
The principle used is that of error control in which the position of a control surface (the output signal) is continually sensed and ‘fed back’ to its flight control computer (FCC). When a command input (the input signal) is made by the pilot or autopilot, the difference between the current control surface position and the apparently desired control surface position indicated by the command is analysed by the computer and an appropriate corrective signal is sent electrically to the control surface. Feedback compensation functions as error control and the FCC regulates the system by comparing output signals to input signals. Any error between the two becomes a command to the flight control surface until output equals input.
In an FBW system the signal route from FCC to control surface is called the forward path while the signal route from the control surface to the FCC is called the feedback loop or path. Gain is the amplification or attenuation which is applied to the forward signal to achieve the desired aircraft response. A filter may be used to block feedback of signals or motion which occur at an undesirably frequent interval.
An advantage of a feedback system such as this is that the flight control system (FCS) can be used to reduce sensitivity to changes in basic aircraft stability characteristics or external disturbances. The autopilot, a stability augmentation system (SAS), and a control augmentation system (CAS), are all feedback control systems.
In a SAS, a damper function is formed in the feedback loop and usually has low gain, or authority, over a control surface. A CAS is implemented in the forward path and represents high-authority 'power steering,' providing consistent response over widely varying flight conditions. The CAS and SAS principles were used independently in military aircraft prior to fly-by-wire, integrated into an FCS, they can operate with more precision and much greater flexibility. Consistent aircraft response is achieved over a broad flight envelope through CAS gains that are programmed as functions of airspeed, mach, center-of-gravity position, and configuration.
Control Laws
The FCCs at the centre of an FCS are programmed with control laws that govern the feedback control system. Control laws are commonly named after the primary feedback parameter as ‘xxx feedback’ or ‘xxx command’. Typical feedbacks are:
- Pitch Channel: vertical load factor ‘g’, pitch rate ‘q’, pitch angle ‘θ’, angle of attack ‘α’.
- Roll Channel: bank angle ‘f’, roll rate ‘p’.
- Yaw Channel: yaw rate ‘r’, sideslip angle ‘b’, rate of change of sideslip angle ‘b with a dot over it’ verbalised as ‘beta dot’).
‘G command’ which is a desirable capability at high speeds, means that for a particular amount of control column force, you get (available energy permitting) the same ‘g’ regardless of prevailing airspeed. Similarly, in a pitch-rate command system, you get the same amount of pitch rate for a given control column force regardless of prevailing airspeed.
To balance the need to communicate pilot commands rapidly whilst at the same time maintaining a context for them as a basis for precision over time, the FCC provides a direct path to the elevator via the ‘proportional line’ or ‘feed forward gain’ but also routes the same command through a parallel circuit ‘integrator’ which produces a control surface command until the feedback signal is equal to the pilot's original command signal. Engineers must ‘tune’ the integrator gain setting so as to prevent excessive lag.
Pure integrator control, or too much integrator gain ‘K’ would cause excessive lag in aircraft response which is why the proportional line is used as well. This arrangement, called 'proportional plus integral' control, is found in most fly-by-wire designs, including those of both Boeing and Airbus.
If undue lag exists in an FCS, causing delay in changing direction from, say, nose-up to nose-down, the effect would be analogous to the human performance lag well known as pilot-induced oscillation or PIO.
An aircraft controlled in pitch by pitch-rate command or g command gives you attitude hold with controls free, similar to the control wheel steering (CWS) feature of an Autopilot. If you change pitch attitude and release control pressure at the desired attitude, the system holds that new attitude because the FCS reacts to bring pitch rate to zero. The aircraft should fly easily with only moderate control forces required and precise attitude control. A consequential benefit of either pitch-rate or g feedback is auto trim in that you can change speed without needing to re-trim for level flight. The same applies to thrust or configuration changes. Auto trim provides apparent neutral-speed stability. Even though positive speed stability was a generally accepted design requirement for conventionally controlled aircraft, the lack of it seems to be acceptable to those flying FBW aircraft with this effect un-moderated. Some FBW types, though, do retain conventional trim 'feel'.
A common control law which blends g and pitch-rate feedback is called C* (verbalised as C star) At low speed in a C* airplane, pitch rate applies whereas at higher speeds, g applies. The changeover is transparent and occurs, for example, at about 210 kts388.92 km/h
107.94 m/s
in Airbus A320 series aircraft. Boeing have made use of a modified C* control law called C*U where U’ represents aircraft forward speed and which provides apparent speed stability. This works by having the trim switches set a reference speed that is summed with the actual speed in the FCC feedback loop in such a way that the pilot feels conventional control force cues as speed changes. You 'trim a speed,' not the pitch control surface. Because the maximum trim reference speed is 330 kts611.16 km/h
169.62 m/s
, a pilot would have to push on the control wheel to further increase speed toward Vmo which conveniently provides a tactile high-speed cue.
Looking in more detail at specific phases of flight, FBW allows designers to optimise the effective dynamics for different flight phases by introducing, for example, an approach mode or a flare mode and creating a multi-mode FCS.

In both the Airbus A320 series and the Boeing 777, the control laws are not fully active until after the aircraft gets airborne because the sensors used for feedback would sense a lot of vibration and ‘noise’ during the take off roll. Landing requires other transitions. Because taking ground effect into account is a ‘one off’ factor in executing a successful landing, the ruling control law may need ‘flare compensation’ to ensure that the usual rearward control column movement is required to flare. In the case of the C* control law in the Boeing 777, an artificial nose-down pitch command is input at 30 feet radio for this purpose. Boeing 777 control laws have also been used to improve the de-rotation characteristics compared to those of the Boeing 757 and 767 by fine-tuning the C*U integrator gain during flight tests. See also the separate article Flight Control Laws, which has more detail on Airbus and Boeing control laws.
System Redundancy?
Rather than providing a conventional FCS for backup, the approach with commercial aircraft normally controlled wholly by FBW is to provide redundancy for the FCCs and sensors by installing more of them. Civil airliner FBW design has generally employed triplex FCSs as is the case with the such as the Boeing 777 and Airbus A340 which both also have limited mechanical backup to allow a period of ‘survivability’ at cruise to sort out any electrical problems. Any duplex FBW systems should be expected to have a full mechanical backup.
When all components are operative, an FCS is commonly said to be operating in normal law. Limited failures usually cause auto reversion to some degraded, but still computed, FCS mode. The lowest level of FBW backup mode normally features analog electronic signals that bypass the FCCs and go directly to the flight control actuators - Direct Law. Under Direct Law, there is no feedback control and there may be fixed gains aimed at providing acceptable control forces proportional to control surface deflection. The gain selected may optimise control forces for the landing configuration, or might provide different gains for cruise and landing, switched, for example, through the flap selector.
Flight Envelope Protection
Feedback control of airspeed, Mach Number, attitude, and angle of attack can be used to ensure that the FBW aircraft stays within its certificated flight envelope. Two strategies have been used to achieve this: the Airbus strategy of` ‘hard limits’ in which the control laws have absolute authority control unless the pilot selects Direct Law; or the Boeing strategy of ‘soft limits’ in which the pilot can override Flight Envelope Protection and so retains ultimate control over the operation of the aircraft.
Accidents and Incidents
The following events included flight envelope protection as a factor:
- A319, vicinity Tunis Tunisia, 2012 (On 24 March 2012, an Air France Airbus A319 Captain continued descent towards destination Tunis at high speed with the landing runway in sight well beyond the point where a stabilised approach was possible. With 5nm to go, airspeed was over 100 KIAS above the applicable VApp and the aircraft was descending at over 4000fpm with flaps zero. EGPWS activations for Sink Rate, PULL UP and Too Low Terrain apparently went unnoticed but at 400 feet agl, ATC granted a crew request for a 360° turn. The subsequent approach/landing was without further event. Investigation attributed the event to “sloppy CRM”.)
- A320, vicinity Tel Aviv Israel, 2012 (On 3 April 2012, the crew of an Air France Airbus A320 came close to loosing control of their aircraft after accepting, inadequately preparing for and comprehensively mismanaging it during an RNAV VISUAL approach at Tel Aviv and during the subsequent attempt at a missed approach. The Investigation identified significant issues with crew understanding of automation - especially in respect of both the use of FMS modes and operations with the AP off but the A/T on - and highlighted the inadequate provision by the aircraft operator of both procedures and pilot training for this type of approach.)
- A321, en-route, near Pamplona Spain, 2014 (On 5 November 2014, the crew of an Airbus A321 temporarily lost control of their aircraft in the cruise and were unable to regain it until 4000 feet of altitude had been lost. An investigation into the causes is continuing but it is already known that blockage of more than one AOA probe resulted in unwanted activation of high AOA protection which could not be stopped by normal sidestick inputs until two of the three ADRs had been intentionally deactivated in order to put the flight control system into Alternate Law.)
- A332 MRTT, en-route, south eastern Black Sea, 2014 (On 9 February 2014, the Captain of a military variant of the Airbus A330 suddenly lost control during the cruise on a passenger flight. A violent, initially negative 'g', pitch down occurred which reached 15800 fpm as the speed rose to Mach 0.9. In the absence of any effective crew intervention, recovery was achieved entirely by the aircraft Flight Envelope Protection System. The Investigation found that the upset had occurred when the Captain moved his seat forward causing its left arm rest to contact the personal camera he had placed behind the sidestick, forcing the latter fully forward.)
- A332, en-route, near Dar es Salaam Tanzania, 2012 (On 27 February 2012, the crew of an Airbus A330 en route at night and crossing the East African coast at FL360 encountered sudden violent turbulence as they flew into a convective cell not seen on their weather radar and briefly lost control as their aircraft climbed 2000 feet with resultant minor injuries to two occupants. The Investigation concluded that the isolated and rapidly developing cell had not been detected because of crew failure to make proper use of their weather radar, but noted that activation of flight envelope protection and subsequent crew action to recover control had been appropriate.)
- A343, Bogotá Colombia, 2017 (2) (On 19 August 2017, an Airbus A340-300 encountered significant unforecast windshear on rotation for a maximum weight rated-thrust night takeoff from Bogotá and was unable to begin its climb for a further 800 metres during which angle of attack flight envelope protection was briefly activated. The Investigation noted the absence of a windshear detection system and any data on the prevalence of windshear at the airport as well as the failure of ATC to relay in English reports of conditions from departing aircraft received in Spanish. The aircraft operator subsequently elected to restrict maximum permitted takeoff weights from the airport.)
Related Articles
Further Reading
- A Simple Summary of the FBW Systems installed on an Airbus A330 is found in: ATSB Aviation Occurrence Investigation AO-2008-070 Final Report, Section 1.6.3 Electrical flight control system (EFCS)
- Airbus fly-by-wire: a process toward total dependability by Taverse, Lacaze and Souyris - Paper presented to ICAS in 2006
- Aviation Safety and Pilot Control: Understanding and Preventing Unfavorable Pilot-Vehicle Interactions, by the US National Academy of Sciences, 1997
Type | Airliner |
---|---|
Configuration | Low wing aircraft, Monoplane aircraft, Retractable gear aircraft, Tricycle landing gear aircraft |
Propulsion | Twinjet (Jet aircraft, Twin-engine aircraft) |
Manufacturer | Boeing |
Author(s) | 787-8 development team
|
FDM | JSBSim |
--aircraft= | 787-8 |
Status | Production |
FDM | |
Systems | |
Cockpit | |
Model | |
Development | |
Website | |
Repository | |
Download | |
Liveries | |
Forum | |
License | GPLv2+ |
The Boeing 787-8 Dreamliner project was aimed at improving the systems and cockpit of the old Boeing 787. Initially undertaken by Omega95 and Redneck, the project led to a major overhaul and redevelopment of the predecessor model, with only the main aircraft model and liveries yet to be modified. An interesting change and key feature of the new model is the impementation of a new Flight Dynamics Model based on the JSBSim. This was created using much data from -- the Piano tool. Other interesting new features include the development of a 'cool' glass cockpit with highly detailed Boeing 787-8 instruments; and many advanced systems such as the Hydraulics, Pneumatics, Heating, Fuel System and Fly-By-Wire functionality.
The first trace of the project on the forum was from the development of the Boeing 787-8's CDU and since then, it has turned into a community project. A lot of developers and forum users have contributed to make this successful. Another key feature is that whenever findings or innovations have been made, they have gone on to the forum and soon, a lot of wiki HowTo tutorials have been created so that these may help other developers too.
- 1Innovations
- 1.4Electronic Flight Bag
- 1.4.3Third-Party EFB Software
- 1.12Airline Flight Management Computer
- 1.13Work on the C++ front
- 1.4Electronic Flight Bag
- 3Systems Overview
- 3.4Fuel Control System
- 3.5Heating System
- 3.7Ground Service Controls
- 8Aircraft Status and ToDo List
New Control Display Unit
A new Control Display Unit (CDU) specifically built for the Boeing 787-8 replaces the generic Boeing CDU and lets you control many of the configurations and settings on the aircraft like VNAV Cruise Settings, the flight plan (with VNAV altitudes,jump to, activate and remove features), Fly-By-Wire Configuration, Departure/Arrival Settings, Electronic Flight Bag (EFB) input etc.
The forum topic for the Boeing 787-8 CDU development can be found in this forum topic.
Functions Accessible through the Control Display Unit:
- Electronic Flight Bag Input
- Fly-by-wire Configuration
- Vertical Navigation Configuration
- Flight(plan) Management Computer
- Automatic Hold Configuration
- Set Terminal Procedures
- Flight Logging System
- Take-off and Approach Reference Speeds (keeps calculation according to weight)
Vertical Situation Display
A Vertical Situation Display [1] is an instrument, part of the Navigational Display (on the MFDs) that show the aircraft's Vertical Navigation Altitudes, Vertical Profile and projects the terrain in front of you. In the Boeing 787-8, it shows approaching terrain for up to 50 miles and also color codes the terrain regions on the basis of danger (red - increase altitude immediately; orange/yellow - advisory; white - safe). The view the Vertical Situation Display, go to the NAV page on any of the MFDs. Note that the VSD is not available on the full-screen ND (NAV page on 2 adjacent MFDs). The VSD is uses a series of Nasal and XML files (which some core developers make like to call 'Hacks') to get functionality of hard coded instruments.
The forum topic for the Vertical Situation Display Development can be found here. [2]Hooray is also working on a Wiki HowTo on implementing the VSD in nasal. Howto: Implement a Vertical Situation Display in Nasal
New Navigation Display
The Boeing 787-8 features a new Navigation Display (ND) which features the ability to plot the waypoints and connect them, like in the real ND. User:zakalawe has been working on a hard coded version of such a display but as we didn't get it at the time, we designed this instrument completely with nasal and XML interactions. Another feature on the Boeing 787-8 is the ability to show a larger Navigation display when both pages are set to NAV on the co-pilot's side MFDs. The larger full screen MFD shows more waypoints and the range can be adjusted between 1 nautical mile and 250 nautical miles. It also shows the airport diagram of the nearest airport positioned and rotated in the right configuration and can be seen better when the range is less than 10 nautical miles.
Another feature of the Boeing 787-8's Navigation Display is a very functional TCAS (Traffic Alert and Collision Avoidance System) which has also been designed completely in Nasal and XML and does not require wxradar to work.
Electronic Flight Bag
Please also see Canvas EFB Framework
The Electronic Flight Bag (EFB) as the name says is like an electronic database of handy documents and charts. The Electronic Flight Bag on board the Boeing 787-8 can calculate the required amount of fuel for your flight, show any airport's (you can search using the EFB INPUT page on the CDU) information, like elevation, metar and runway information like heading, length, ILS frequency), connect to Virtual Star Alliance's Automatic PIREP System for more functionality, connect to Redneck's FGFSCopilot for logging, show the GPS settings (your position on the world map, course and true headings to your next way-point and distance to your next waypoint. It also has realistic checklists for every phase of the flight, and an operating manual explaining basic maneuvers. You can also 'INSTALL' airport diagrams and charts into the '/787-8/EFB-DB' folder which allows you to view them on the CDU (searchable using the EFB INPUT page on the CDU).
Quick Guide to install and view airport Diagrams
> Download diagrams from any source, convert them to *.jpg format and rename them '<icao>.jpg'. Then, place them in the EFB-DB folder. Then, use the 'EFB INPUT' page on the CDU to enter the airport ICAO and it displays the diagram on the EFB.
Quick Guide to install and view SIDs, STARs and IAPs
- Download the chart you need from any source (I use http://www.airnav.com for US charts and http://www.opennav.com for others), and convert the chart to *.jpg format. (if it's pdf, a good idea is to open it in full view and take a screenshot :wink: )
- If the airport and chart type folder doesn't yet exist inside the EFB-DB/Charts folder, create them like (for example I want to install the 25L-ILS IAP chart for KLAX) /EFB-DB/Charts/KLAX/IAP/
- Now, rename your *.jpg file to the chart name (eg. 25L-ILS.jpg) and place it inside the '/EFB-DB/Charts/KLAX/IAP/' folder.
- Now, open the /EFB-DB/ChartsList.xml file and add in your chart data (use the older charts' data for the format)
- Start up the 787, go to the 'Airport Charts' page on the EFB, go to the 'EFB INPUT' page on the CDU and
- Enter the Airport ICAO and press on the button next to 'Airport ICAO (Enter)' label (or the space under it on the touch-screen CDU)
- Click on the button next to the 'Chart Type (Select)' label to cycle through SID, STAR and IAP
- Click on the button next to the 'Chart ID (select)' label to cycle through available charts.
- Now, hit the 'DISPLAY >' button on the CDU and look at the EFB to see your chart.
Note that for some charts, the orientation may be land-scape and not portrait. But to overcome that, I've put a 'ROTATE' option on the EFB which rotates the chart when you click it.
The Above has been taken from the forum topic.
Third-Party EFB Software
The Electronic Flight Bag is also meant to provide and interface third-party and/or operating airline softwares. These are not present in the Flight Management Computer by default but we're working on a couple of softwares for the EFB. This is not unrealistic because this is one of the main purposes of the Electronic Flight Bag. Here're the softwares we're working on for the EFB.
FGFSCopilot Logger
The FGFSCopilot is a java program that can do almost everything required from taking off till landing the plane at your destination. The Boeing 787-8 has an FGFSCopilot Log page in the EFB which shows it's connection status and every log message the FGFSCopilot sends to FlightGear.
VNAV Automatic Altitudes Generator
The VNAV AutoGen is a third party software on the EFB that automatically calculates ideal vnav altitudes for the active route. To use it, simply create/load a flightplan, copy it to the active route, go to the VNAV Altitudes Gen page on the EFB and click on AUTOGEN >. That would generate altitudes for you which're displayed on the EFB. You can scroll through the waypoints using SCROLL UP > and SCROLL DOWN >. Finally, if you're happy with the automatically generated altitudes, click on COPY TO RTE > to move them to the active route.
Fly-By-Wire System
The Boeing 787-8 Dreamliner is FlightGear's first Airliner to feature a complete Fly-by-wire system. The idea behind this fly-by-wire is to get it the pilot's controls (/fdm/jsbsim/fcs/x-cmd-norm : where x can be aileron, rudder or elevator) and work with it and give out another output property (/fdm/jsbsim/fcs/x-fbw-output) which is read by the FDM and control surface animators. The throttles don't have a chain such as the other surfaces so that the pilot can easily override the fly-by-wire (one of Boeing's 'philosophies'). At this stage, the fly-by-wire can protect the aircraft from extreme bank angles (flight envelope protection- roll) where the bank angle limit can be set by the pilot in the CDU's 'FBW CONFIG' page, protect the aircraft from extreme alpha angles (flight envelope protection- alpha), calculate the throttle required and set it accordingly to maintain profile on turns, reduce throttle to stay under limits and finally auto-stabilize the plane and maintain the current profile when the yoke is brought back to the center. The Fly-by-wire also dampens the control to prevent any sudden motion. Fly-by-wire can be toggled from the CDU's 'FBW CONFIG' page.
NOTE : To be able to activate alpha-protection, roll-protection and auto-stabilizer, you need to be atleast higher than 3500 feet. This is so that the fly-by-wire doesn't interrupt your approach.
We've also created a tutorial which shows how you can implement the fly-by-wire we wrote for your aircraft : Howto: Implement a Fly-By-Wire System for Airliners
Automatic Vertical Navigation
I've seen a lot of wiki pages on aircraft autopilot and always noticed that next to 'VNAV -' the author writes either he doesn't know what it is, or it doesn't do anything or he hasn't tested it yet. Well, for a change, here I'm telling you what the VNAV does.
We have designed the autopilot route manager in the CDU to be able to accept VNAV altitudes for each (or whichever you want) waypoint. On the Dialog Route Manager, enter your waypoint in the format 'WP@ALT' for example, 'KSFO@9000'. So let's say you have different altitudes according to your SID/STAR/IAP till cruise altitude and then different altitudes for your waypoints when you land. Let's assume your flight plan to be:DEP, WP1@3500, WP2@10000, WP3@18000, WP4@26000, WP5, WP6, WP7, WP8, WP9, WP10, WP11@20000, WP12@12000, WP13@8500, WP14@4000, DEST
You doesn't have to enter altitudes for WP5 to WP10 because you'll start cruising at WP5 (say you want to cruise FL360 aka. 36000 ft) and stay at 36000 ft till WP10. That means WP11 will be your 'End Cruise' Waypoint, where you aim at when you're out of the cruise.
To set cruise settings, go to the CDU's 'VNAV' page and enter cruise altitude in the respective area. Then enter your cruise start altitude (in this case, WP5) and cruise end altitude (in this case, WP11) in their respective places (there're labels).
Once you're ready, finish other checklists, take off and turn on 'LNAV' and 'VNAV' on the Autopilot. The VNAV is designed to automatically calculate the required/ideal climb/descent rate to get to your waypoint just in time. Out of all the tests we've conducted, the VNAV is VERY accurate at the moment.
Flight-plan Management System
In the Feb 25th, 2012 git commit, a new flight-plan management system has been written for the Flight Management Computer(s). The new system, like the real one lets you put in 2 flight-plans (with altitudes), and an alternate airport. You can do everything that you can to the route manager on these 2 flightplans. Boeing likes to call them Primary Flightplan and Secondary Flightplan. Once you enter your primary and/or secondary flight-plan, the respective flight-plan's status will show READY on the flight-plan management page. Then, a new option, COPY TO RTE will appear under the respective flight-plan and on clicking that, that plan will be moved to the active route. To make any changes to the route, you can either make them to the flight-plan and copy them to the route again or simply work with the active route by clicking on the ACTIVE ROUTE option in the Flight-plan Management page. An alternate airport is recommended to be entered in the CDU so that in case there's a problem during flight, the plane can be automatically be diverted (by the FMC) without you having to do anything other than pressing the DIVERT option on the Flight-plan management page. Note that using the DIVERT button to divert to your alternate airport clears your active route and sets the aircraft on a direct flight to the Alternate Airport.
Automatic Holding Pattern
The Boeing 787-8 now features an automatic holding pattern system where you enter the hold fix/navaid, hold radial and hold leg time and the aircraft automatically flies in a holding pattern there. (as described in real Instrument Flight Rules Rating Course (IFR) textbooks) This feature is still being developed at the moment and is not perfected, but it still does the basic thing for you.
We have tested this feature from KIAH (George Bush Intercontinental Airport, Houston) holding at the VOR, LOA (LEONA VORTAC, about 70 miles north-west of KIAH) at a hold radial of 0, and hold leg time 120 seconds. We've been able to hold and re-trace the hold path every lap, but we get a strange shape due to the pid-controller. We're still working on it.
Traffic Alert and Collision Avoidance System
The Boeing 787-8 Dreamliner (as of February 21st, 2012 on GIT) features a brand new TCAS (Traffic Alert and Collision Avoidance System) which has a capability of showing 30 Multiplayer aircraft and 20 AI Aircraft on it! Now, you won't have to complain about not seeing all aircraft on VATSIM ;) We're still working on increasing it's capability to 50 each multi-player and AI.
The TCAS has 3 different symbols for each aircraft and 4 different color codes. Each aircrafts' callsign, altitude and true airspeed will also be written next to the sprite.
- The Diamond Shaped Aircraft sprite shows that the aircraft is flying level.
- The Box with Up Arrow shows that the aircraft is climbing.
- The Box with Down Arrow shows that the aircraft is descending.
- A Cyan or Blue Colored Sprite shows that the aircraft is at a safe distance.
- A Yellow Colored sprite shows that you need to be aware of traffic nearby.
- A Orange Colored sprite shows that you need to either change altitude or course, consult ATC. It is an advisory.
- A Red Colored sprite shows that you are in danger and immediately need to follow the TCAS instructions.
The TCAS is configured to sound voice alerts according to the situation. The TCAS voice alerts needs to be followed over the ATC's instruction if they contradict. The TCAS will alert you if you are in danger of collision with MP or AI Aircraft.
NOTE: The TCAS voice alerts have been confirmed working on FlightGear git (2.7, as of February 19th, 2012) but don't seem to work in FlightGear 2.4.
Terrain Map and Weather Radar
The Boeing 787-8 Dreamliner (git version as of February 21st, 2012) features a terrain radar which creates a terrain map on the MFD when the Navigational Display is set to TERR mode (you can change the mode from the buttons on both sides of the Mode Control Panel). Click on WXR to view the WXRadar (Collins WXR-2100), TERR to view the Terrain Map and CLR to clear the ND. The weather radar is still under development and a working version is not available, but the terrain map uses a 'get little and interpolate' method to create smooth terrain mapping.
World Map and Flight Path Plotter
Another option to put on the ND is the world map. It's not exactly a terrain map, but rather like satellite imaging. The plane is shown (it's zoomed in) on the map and the plane's path is marked with fading red dots. You can get your ND to show the satellite maps by pressing the WMAP button on the ND mode panel. Note that you can have any 1 of WXR, TERR or WMAP on and to remove them, press the 'CLR' button.
Airline Flight Management Computer
The Boeing 787-8 Dreamliner is an Airliner and we can't leave out some of the key features airline manufacturers put in their aircraft. There're 2 major sections in the Flight Management Computer (it's a part of the CDU) - the ROUTE and DEP/ARR. Both pages are accessed from the CDU(s). The Route is directly connected to the Route Manager and doesn't do anything 'special', but the DEP/ARR page lets you work with preset routes, SIDs, STARs, IAPs etc. You can enter the flight number (this is meant for virtual airlines: By default, Merlion's Boeing 787-8 Routes are included in the Database but I'll make a tutorial on how other airlines can put in their data) and be able to search for the flight information. If the airline has specified a Route and/or VNAV Altitudes and Configuration, you can load up those preset routes and altitudes by pressing the 'SET ROUTE >' menu. If a preset route doesn't exist, the FMS will generate a route automatically. A pilot does not have to worry about preset/generated routes. Another feature in the FMC is Scott Hamilton's LevelD-767 NAVDATA Parser, which gets SID/STAR/IAP Data and automatically puts them in the right place in the route manager for you to be able to fly them. This data can be managed from the PROCEDURES option in the DEP/ARR page.
A much more detailed tutorial of how to use preset routes and automatically set terminal procedures is available in the wiki sub-page: Boeing 787-8 Dreamliner: Flightplan and Procedures Tutorial
We'll also be creating a video tutorial (Dreamliner Tutorial #6) on the Flight Management Computer.
FMS Navigational and Terminal Procedures Data
The Boeing 787-8 Dreamliner and the Airbus A380 (being developed by Scott Hamilton) uses Scott's Level-D 767 NAVDATA Parser to get Navigational Data and Terminal Procedures into the aircraft's Flight Management Computer (Flight Management System on the A380). The FMS Data must be downloaded separately.
By default, the 787-8 contains navigational data for the following airport - WSSS, YBBN, KLAX, KJFK, EGKK for testing purposes and as the Flight Management Computer Tutorial is a flight from KLAX to KJFK.
Work on the C++ front
The capabilities provided by this aircraft touch many parts of FlightGear, that will benefit from modifications to the C++ code, this is an attempt at documenting useful C++ work. Most of this should probably be posted to the issue tracker, too.
Backup 2 Fbw Custom
Camera/Video Surveillance Instrument
The Aircraft doesn't 'yet' have a camera/video surveillance instrument but the team is working on it. We are creating a Wiki Howto: Use a Camera View in an Instrument while working on it so our progress can help other aircraft developers. The basic idea is the render the camera view to texture and get flightgear to display it on the instrument. As this instrument includes work in C++, it will NOT be available in FlightGear 2.4.0 or 2.6.0, and not even git at the moment.
Backup 2 Fbw Mini
Creating a 2D drawing API
Also see Howto: Create a 2D drawing API for FlightGear.
Increasing the range of geodinfo()
Fix geodinfo() so that it may provide access to tiles not yet loaded, i.e. tiles that are not 'visible' (which is the limiting factor currently). This will also be useful for the local weather system and probably a number of related scripts.
The tile manager is capable of satisfying multiple requests. Anyone can give it a position, range and a timeout. It will then try to load all tiles in the range specified. And it will stop loading them after the timeout - unless you have updated the request with a new timeout. So you could tell it every 5 seconds that you're interested in a certain area around the aircraft, and use a timeout of 5,01 seconds. A matter of memory and loading speed though.[1] — Thorsten Brehm |
The Boeing 787-8 Dreamliner has a very complete and realistic modern glass cockpit based of the real Boeing 787-8 cockpit. Almost all of the instruments (excl. Weather radar which is currently coming up, and the voice comm.) are functional and work like the real thing. Multiple views have been created (like the OHP, CDU, EFB, Full Cockpit Views) so that pilots can easily work on different parts without looking away and adjusting view position.
That's all I can say about the cockpit now... You better test it out to judge it.
Electrical System
The Boeing 787-8 Dreamliner uses a modified version of Syd Adam's Jet Electrical System. Backup Generators have been added, a Ram Air Turbine Generator has been implemented and the APU loop has been modified. There are 5 major power sources available are:
- Engine Generators (L1 and R1 are main generators and L2 and R2 are backup)
- Battery
- Primary and Secondary External Power
- APU Generators (Auxiliary Power Unit must be started and running for the APU Generators to provide power)
- Ram Air Turbine (used in case of dual engine failures to provide just enough power for Central Hydraulic Systems (C1 and C2) and Instruments.
To Understand the Electrical System better, take a look at the 'ELEC' page on any of the MFDs on board.
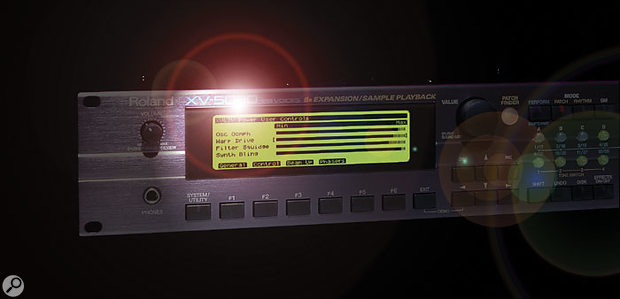
Hydraulic System
The Hydraulic System on-board is very advanced and does the job it's supposed to do.There are 3 basic Hydraulic Systems - Left Engine Hydraulics, Right Engine Hydraulics and Central Electrical Hydraulics. Both Left and Right Engine Hydraulic Systems are pressurized by Engine pumps which require the engines to be running. These pumps pressurize the L and R systems that are connected to the flaps, spoilers, brakes and landing gears. Therefore, you need atleast 1 of the 2 Engine pumps to be running to be able to use these. But, the landing gear has an 'alternate gravity drop system' which you can use to get your gear down in case of a hydraulic failure.The Central System has 2 electric pumps that control pressure to the hydraulic system that controls the ailerons, rudder and elevators. Only 1 of the 2 pumps have to be turned on at a time, and the other can be used as backup in case of a failure. The hydraulic pumps can overheat and fault if not adequately cooled, refer to the 'Pneumatics and Air Conditioning System' for more information on this.
To Understand the Hydraulic System better, take a look at the 'HYD' page on any of the MFDs on board.
Pneumatic System
The Boeing 787-8's pneumatic and Air-conditioning system controls bleed and flow of air through packs (and trim) which are then used to cool the equipment on board. The pneumatic system is pretty simple, you have 2 packs, 2 trim air controls, a gasper, and engines and APU bleed. The 787's systems automatically control bleed according to what is required and available, but you'll have to control the trim and packs. Equipment Cooling is an option on the Pneumatics panel which passes cool air into the hydraulic and fuel pumps to prevent them from overheating. When a pump overheats, you get a warning and if you do not either turn it off or switch on equipment cooling, the pump can fault. The 'PNEU' page on the MFDs show you more information on equipment temperatures and Pneumatic settings.
Fuel Control System
The Fuel Control System let's you control the 7 fuel pumps on board the 787-8 Dreamliner (2 Left Tank Pumps, 2 Central Tank Pumps, 2 Right Tank Pumps and a Crossfeed pump). The left tank and central tank pumps pump fuel from these tanks to the left engine, while the right tank and central tank pumps pump fuel from these tanks to the right engine. In case of a fuel imbalance, you can turn on the crossfeed pumps to transfer fuel from the tank with excess fuel to the one with low fuel.
Fuel Jettison
The Aircraft has a complete fuel jettison system where you can select which wing nozzle to jettison from, arm jettison and use a knob to define the dump rate. If the Left Nozzle is activated and Fuel Jettison is armed, you dump fuel from the left and central tanks, and the same for the right nozzle. Note that the 787 will NOT let you dump fuel if you have less than a critical value.
Heating System
The Heating System on board controls 4 different heating equipment. First of all, let's get into 'natural icing'.
Natural Icing at certain Conditions
If your TAT (Total Air Temperature) value is under 10, your wings, engines and wind shield can start picking up ice. Window Ice simply forms on the window and obstructs your view out of the cockpit. Whereas, wing ice actually affects your lift and drag in the FDM! As for engine ice, if you have extremely high amounts of ice, the engines can fault and you might have to cool and then restart them.
Note that Engine surges are NOT due to ice build up. If you get an engine surge while flying, you might either be flying over Vne, or in extreme weather conditions with N1 above safe limit in those conditions.
The Aircraft's way of Taking care of Ice
The Window Heating switches on the overhead panel enables a heater to start melting the ice on the windshield letting you see outside clearly.
The Anti-Ice knobs (2 engine knobs and a wing anti-ice knob) let you control the heating equipment on the respective areas.
The 'HEAT' page on the MFD should have more information on the Heating Systems.
Gear System
The Boeing 787-8 dreamliner has 3 retractable gear units, the nose gear has 2 tires, and the main landing gears have 4 each in a square layout. The gear system manages gear compression and failures (stuck, tires burst and break off) on the basis of airspeed, wow and compression.
The gears system can be monitored from the 'GEAR' page on the MFD(s).
Ground Service Controls
Fuel Truck
The fuel truck (MENU: Boeing 787-8 > Fuel Truck Controls) can be enabled/disabled and connected/disconnected from the aircraft's fuel value under the wing. You can enter an amount of fuel in the request fuel quantity input and ask the truck to re-fuel the aircraft to that quantity. You can also ask it to drain the fuel tanks.
De-icing Truck
The de-icing truck along with the other ground services can be controls from the Ground Services Controls menu (MENU: Boeing 787-8 > Ground Services Controls). The de-icing truck can be enabled/disabled and you can also de-icing the aircraft. The de-icing process includes the truck animations and actually de-icing the aircraft!
External Power Box
The External Power box is a stand-alone generator that provides external power to the aircraft. When enabled, it is connected to the external power socked under the aircraft's left wing. Note that this needs to be enabled so that you get external power. When you start FlightGear, the external power will be enabled by default.
Landing Gear Chokes
Landing Gear chokes are triangular prism shaped blocks that're placed in front of and behind the landing gears to prevent the aircraft from moving. These chokes will also prevent the aircraft from moving in FlightGear and are enabled by default on start up. Note that to get the aircraft moving, you need to remove the parking brakes and chokes.
Catering Truck

The catering truck can be enabled/disabled and toggled. The Toggle Catering option is to lift/lower the catering box and connect to the the R1 Door. It doesn't do anything else.
Baggage Ramp and Trailers
These're just models and don't do anything at the moment.
System Failure Simulation
The aircraft has a built-in failure simulation dialog where you can get different systems to fail in different ways. The failure simulation dialog can do the following:
- Flame-out any of the engines
- Fail any of the engines
- Set any of the engines on fire
- Burst any of the Wheel Tyres
- Have a gear unit break-off
- Stuck a gear unit in it's current position
- Fail individual hydraulic systems
- Overheat any of the hydraulic or fuel pumps
- Fault any of the hydraulic or fuel pumps
Other general failures like Electrical, Static etc. have not been implemented in this dialog as they can already be controlled with FlightGear's Generic System Failures dialog.
NOTE: When you flame-out an engine, it can be restarted, but not in the case of a failure. Faults just means that the pump is too hot to function, but it can be restarted when cooled.
IMPORTANT!
- In case of an engine surge, (this cannot be toggled by user as it requires certain weather conditions and N1 to occur) immediately reduce throttle and get the N1 under 65%. If you're flying too fast, try to slow down and avoidance extreme weather (heavy rain and snow) would be a nice idea if you want to prevent surges.
- In case of an engine fire, pull the respective engine's fire extinguisher lever (it's right behind the throttle quadrant) and cutoff fuel to that engine. If the fire persists and you don't extinguish it, the engine may face an explosion and severe damage will be inflicted, leaving that engine unusable (basically, you can't restart it)
Johan G posted in the Boeing 787-8 Dreamliner Forum Topic:I really see why there could be a real need to have a copilot along when 'flying in' the aircraft during pilot conversion.
Basically, the systems are very complex that it might be difficult for just 1 person to control the plane and manage the systems. As an immediate solution, the virtual copilot can announce ref. speeds, control flap lever, control gear lever, control heating and pneumatics, set altimeter setting and engage thrust reverser's and spoilers on touchdown. You can select exactly what you want him to do in the Virtual Copilot Settings Dialog.
On the other hand, we're working on a new advanced dual control system which allows the copilot to completely control the aircraft and see all instruments over multiplayer.
See the Aircraft/787-8/
directory in FGAddon.
Thanks to Oscar [3] for the amazing Aircraft of the Month Review Video for the Boeing 787-8 Dreamliner.
Flight Dynamics Model: 4
- The Boeing 787-8 has a JSBSim FDM matching a lot of results from http://www.lissys.demon.co.uk/samp1/desmis.html
- We don't have more detailed test results. so we can't test everything yet. Once we get that, we need to tune the FDM further.
Aircraft Systems: 5
- The Aircraft has very advanced systems imitating realistic systems from the real 787.
- Random/Checkable Failures purposely haven't been implemented as random is never realistic. But Engine failures, ice etc. occur in the appropriate conditions.
- The 787-8 has very advanced instruments, flight management computer, hydraulic, electric, pneumatic, heating, fuel etc. systems.
Cockpit and Instruments: 4
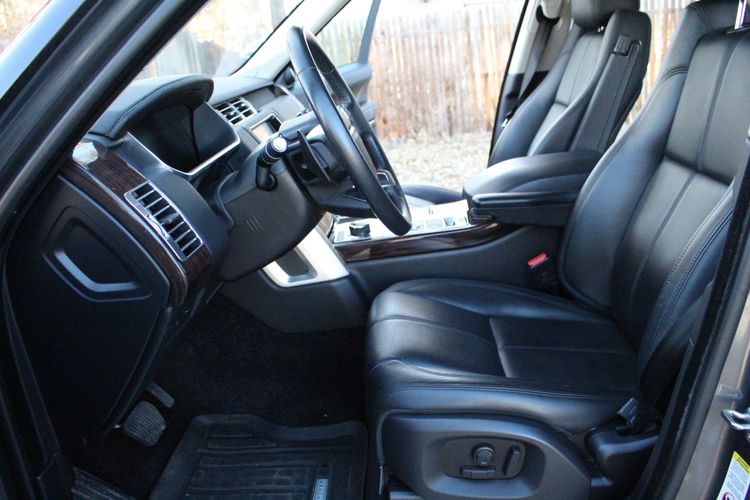
- The cockpit is very detailed and most buttons are there and functional.
- The instrument displays are very advanced and functional, the ND could be replaced by a hard coded version though.
- A Camera View instrument is supposed to be there but isn't, but we're working on a hard coded camera view instrument.
- The aircraft uses textures extracted from pictures and ambient occlusions created with blender.
- The complete cockpit has been light-mapped and looks very good at night too.
Model: 4
- The model is still from the old 787-8, there's the basic model without a cabin, rods aren't yet complete either.
- The landing gears have been re-done and look a lot better now, but the model has a much better scope of improvement.
- The Model Rating has been taken right out of the old Boeing 787-8
There are plenty of tutorials and code snippets that were specifically created for this project, this is a list of all things related:
References
|
|
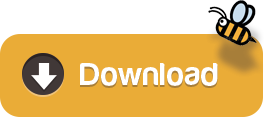